14 causes of submersible pump and motor failure
Submersible Pump and motor failure can result in extended downtimes, repeated repairs, and higher maintenance costs. submersible pump and motor failure cause understanding can help in the selection of the pumping equipment.
Here, we look at the 14 Most Common causes of submersible pump and motor failure is described below
1.Cavitation
It is the rapid creation and subsequent collapse of air bubbles in a fluid. When the Net Positive Suction Head Available (NPSHa) is lower than the Net Positive Suction Head Required (NPSHr). Pump cavitation can cause a number of issues for your pumping system, including excess noise and energy usage, not to mention serious damage to the pump itself.
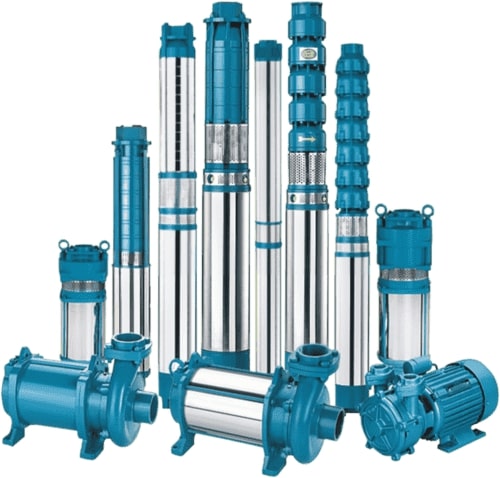
2.Reverse Rotation of Motor
This will occur when the pump is wired incorrectly due to the motor will rotate in the reverse direction. When a motor starts rotating reverse, very little water will be pumped but it does serious damage to the pump, polishing the impeller and leading to cavitation.
3.Overheating
The most common reason for failure in a Submersible Motor and pump is Overheating, as this causes the insulation materials in the motor to deteriorate until failure occurs.
4.Dry Running of the pump
This happens when water level drops to a point where the pump cannot draw a decent amount of water and/or starts to create a lot of disturbance in the water.
Submersible pump dehydration running time is not too long.
This will quickly lead to cavitation, damaging the impeller and diffuser, and quickly destroying the pump. It also causes the seal rubbers to dry out and crack which allows water into the motor.
5.Humidity and Moisture
Moisture and humidity in the air can wreak ruin on your electric motor, especially over time. By themselves, they can cause corrosion inside the motor or pump.
6.Cable Damage
This includes internal damage often unseen when the cable is damaged externally. It is vital that if a cable has been gashed or yanked that this is checked. The seal arrangement where the cable enters the pump body is a weak spot and the air seal can very easily be broke
7.Dead head cause pump shaft break
This is where the pump has a more vertical head than it is designed for, i.e. a valve on the discharge has been closed. This causes something called discharge cavitation which is indicated by the sound of marbles being pumped and pitting around the impeller tips and inside of the pump casing. At an extreme this can make the pump shaft break.
8.Not allowing for Discharge Piping
Discharge piping creates friction loss and it is vital that this calculation is taken into account when specifying submersible pumps. Otherwise, it will lead to deadheading.
9.Mechanical seal damage and leakage
Often use insulation resistance tester to check the submersible pump insulation resistance, the occurrence of insulation resistance is reduced in time to take maintenance measures, it will not happen to burn the motor.
10.Lack of work
In the absence of work, the submersible pump is generally in the braking state, the current is much larger than the rated value when the submersible pump winding temperature increases, it lasts for a long time, it will burn the stator windings.
11.Impeller stuck
When the impeller is locked, the current increases over the rated value for a long time and the stator windings of the submersible pump will burn out soon.
12. Dust and Contamination
An electric motor is quite efficient at drawing in dust particles from the atmosphere as it runs. Once the particles reach the inside of the motor, they can cause a lot of damage and failure. This is dependent upon the size and physical properties of the particles.
13. Running on the Right of the Curve
This is where there is less vertical head than the pump is designed to handle, which makes the pump less efficient.
14. Specific Gravity
The pump is not designed to deal with high levels of solids and will usually quickly fail in slurry applications.